Leading the fourth wave
To stay at the forefront of Industry 4.0, Lockheed Martin partners with higher education to teach and inspire a workforce that will work with machines as partners.
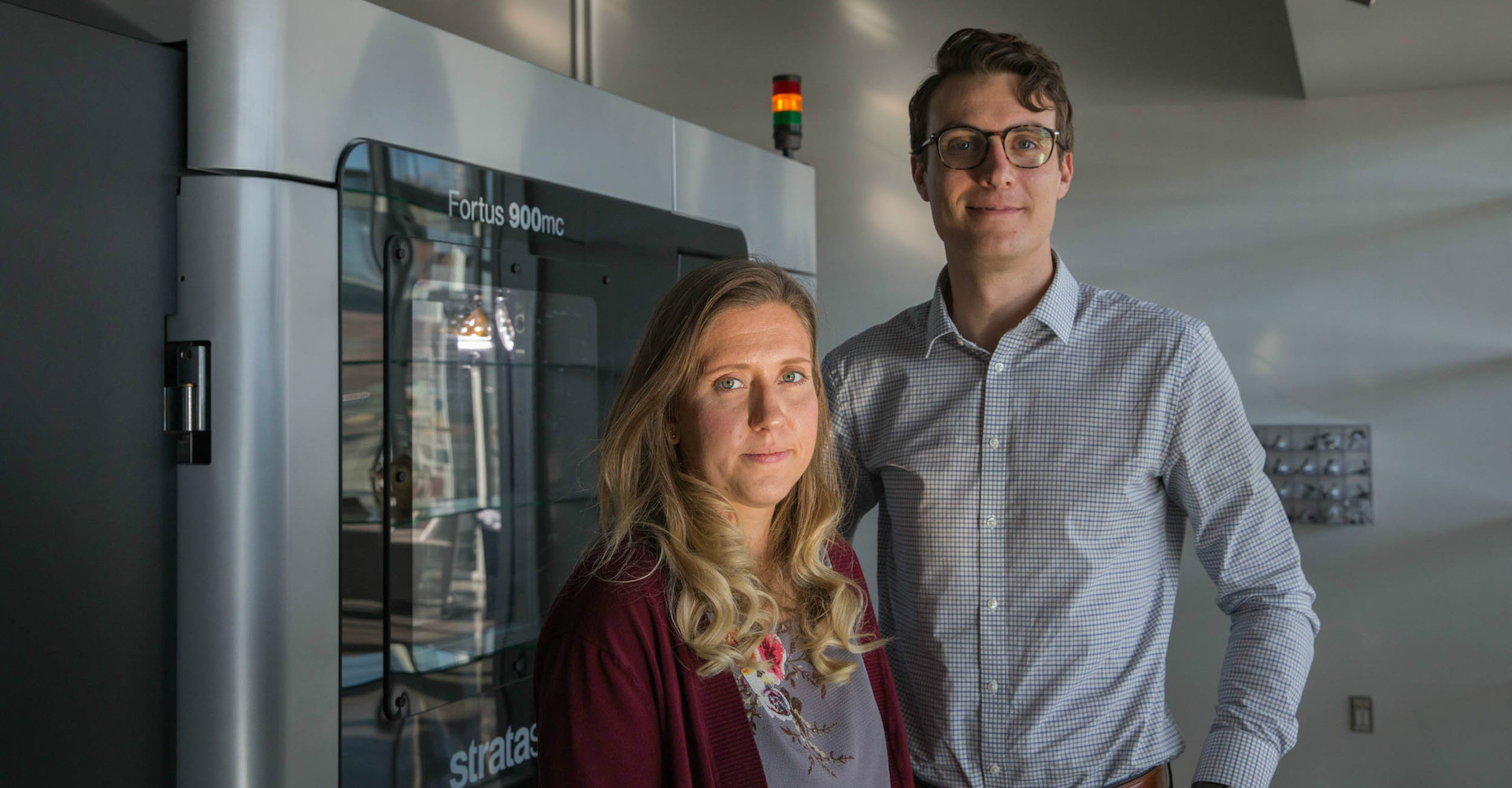
America’s aerospace manufacturers are rocketing into Industry 4.0, or the Fourth Industrial Revolution, a digital manufacturing economy powered by data.
Lockheed Martin Space of Colorado is at the forefront of that revolution, recognizing that the future of their work will be defined by artificial intelligence, human-machine teaming and data as a strategic commodity, Jeff Wilcox, Lockheed Martin vice president of digital transformation explained to The Atlantic Festival last fall.
“There is a new art and science being born at the human-machine interface,” Wilcox said. “It’s where we meet data, where we access data, how we shape data – and it’s where we leverage data.”
As it builds and transforms its workforce for Industry 4.0, Lockheed Martin is turning to Metropolitan State University of Denver students to drive innovation on the company’s Waterton Canyon campus and in laboratories on the MSU Denver campus.
Every year, Lockheed Martin recruits MSU Denver Advanced Manufacturing Science students for its co-op program at its satellite production facility. The part-time, paid position helps students fulfill degree requirements and gain job experience; the company gets students’ fresh perspectives on advancing Industry 4.0 goals and access to a trained pool of prospective employees, said Mark Yoss, Lockheed Martin production principal and co-op director.
The aerospace giant also recently invested $1 million to help establish the University’s Lockheed Martin Additive Manufacturing Laboratory, which is centered around the Stratasys Fortus 900mc, a state-of-the-art 3D printer that is a big part of the company’s Industry-4.0 future. The investment also established an endowed director of the Advanced Manufacturing Sciences Institute, a position held by Robert Park, Ph.D., who oversees the Advanced Manufacturing Sciences degree program and serves as a liaison between the Institute, Lockheed Martin Space and other industry partners.
Last fall, Park brought Brian Kaplun, Lockheed Martin additive manufacturing manager, to campus to teach the institute’s first class utilizing the 3D printer. This spring, he brought Lockheed Martin computer numerical control machining expert Richard High to campus to teach a course on CNC machining and inspection focusing on the subtractive side of advanced manufacturing.
“Having industry experts such as (Kaplun and High) engaged with our AMS curriculum as instructors exposes our students to subject matter at a state-of-the-art level,” Park said.
Identify problems, develop solutions
On Lockheed Martin’s Waterton Canyon campus, co-op students are assigned to “Operations Excellence Teams” tasked with rethinking operations by identifying problems and developing solutions, Yoss said. The problems they face range from gluing microscopic computer chips in place to tracking tools used in the manufacturing process.
Ben Terry, an Advanced Manufacturing Sciences major who graduates in May, has already been hired by Lockheed Martin, in part because of his work in the co-op program, Yoss said. The future microelectronics manufacturing engineer spent his co-op solving a sticky issue: how to best affix critical chips as small as three one-thousandths of an inch in their proper position within a satellite.
Affixing such small pieces in place is accomplished with a machine that applies a minuscule dot of epoxy to a surface. However, forcing that epoxy through a hollow needle produces irregular dots. To eliminate those irregularities, Terry developed and is currently testing a promising solution in which a machine dips a tiny stamp in a well of epoxy and then stamps out a pattern upon which the diminutive chips are affixed.
“To validate the solution, we have a bunch of glass slides cut to the same size as our components and we’re using them to see if there’s enough (epoxy) coverage underneath,” he explained.

Emilie Vaughn, an Advanced Manufacturing Sciences major graduating this spring, worked in a team building spacecraft parts such as the so-called “black box” that distributes power throughout a satellite. She helped solve several critical problems during her co-op, including one that improved the efficiency with which satellites are manufactured, Yoss said.
When she began her co-op in early 2018, technicians assembling a satellite protected exposed wiring by covering metal frames with tape manually cut into precise lengths and shapes. Vaughn helped acquire and program a new tape-cutting system that slashed the time it takes to complete the task by 40%.
Vaughn also helped solve a tool-tracking issue utilizing technologies old and new, Yoss said.
To create accountability and flow for critical tools, she helped implement a simple shadowboxing system in which an image of each tool is put on the bench or tray on which it should be kept when not in use. She also helped develop a photo checkout system to show which employee has what tool and where it is being used.
The tool-tracking solutions increase efficiency by limiting the time technicians spend looking for tools – and ensuring that satellites are ready for launch at delivery.
“It’s like in an operating room: You don’t want to leave anything behind inside,” Yoss said of the tools involved in the satellite manufacturing process.
Fresh perspectives on 3D printing
Back on the MSU Denver campus, students are already making waves with a technology Lockheed Martin views as critical to its Industry 4.0 future: 3D printing.
“Additive manufacturing enables cost and schedule savings across all of our platforms and technologies, allowing new and exciting solutions to both legacy problems and those of the future,” Lockheed Martin’s Kaplun said.
As part of its investment of $1 million to establish the Lockheed Martin Additive Manufacturing Laboratory, the company donated to the University a Stratasys Fortus 900mc, the same 3D printer at use in its Waterton Canyon campus. Last fall, Kaplun taught the new class Introduction to Additive Manufacturing Stratasys Certification Preparation.
The goal of the class wasn’t just to help MSU Denver students earn certification for an industry-leading 3D printing system, he said. It was also to introduce the technology to a diverse collection of minds that may approach 3D printing with new perspectives. And in that regard, the class was a complete success.
“The class drew individuals throughout a diverse range of ages, backgrounds and prior experiences,” Kaplun said. “Overall, 17 students passed the certification exam out of 19 – far above the typical average and something that MSU Denver can be justifiably proud of.”
The final projects were a testament to the diversity of those students, he said. There were complex mechanical transmissions, animal scenes and mechanisms capable of taking flight under their own power – all built in one piece on the Stratasys Fortus 900mc.
The class award for Most Artistic Design and Best Overall Design went to Noah Rouzaud for his intricate 3D-printed carousel, complete with “galloping” horses moved up and down via internal gearing; Rouzaud graduated last December as the first MSU Denver student to earn an Advanced Manufacturing Science degree.

“The students created works of art that approached engineering problems in a physically beautiful manner, unlike what is commonly seen in engineering circles,” Kaplun said. “This is particularly important because (Lockheed Martin) needs different thinking to advance our spacecraft design with additive manufacturing. When we design with full-systems thinking in mind, we can merge parts into the structure; create different material patterns to reduce mass or add strength; and we can make spacecraft smaller and lighter so that they are less costly to launch.
The class doesn’t just provide Lockheed Martin with a glimpse of how new and aspiring engineers approach this important technology; it also trains a future 3D-printing workforce, Kaplun said. Building that workforce is a critical goal for the company, which views 3D printing as a key enabler in achieving its goal of building satellites twice as fast and at half the cost.
“In the last two years, our thousands of flight-qualified additive parts yielded an average of 85% cost reduction and 90% schedule savings,” Kaplun said.
In his closing remarks at The Atlantic Festival last fall, Lockheed Martin digital transformation VP Wilcox emphasized that unlike previous industrial revolutions, Industry 4.0 “isn’t about the stuff, it’s about the people.” The company’s goal, he said, was to build and train a technology-focused workforce wherein people “work to their full potential and bring their full selves to work.”
With 23 former co-op students landing jobs at Lockheed Martin in the last four years, and the creation of a cutting-edge Advanced Manufacturing Sciences degree program, MSU Denver graduates are well positioned to be at the forefront of the workforce that will launch the aerospace industry into the 21st century.